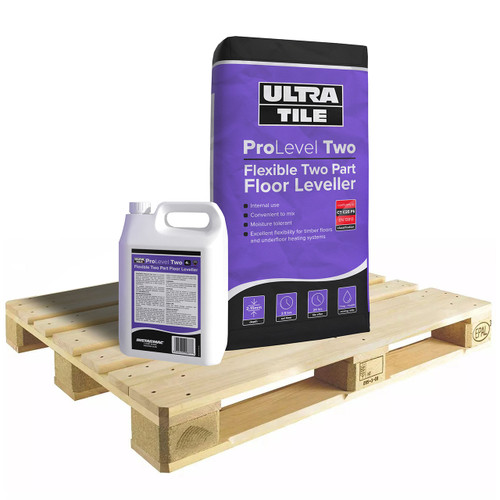
Ultra Tile Pro Level Two - High Flow Floor Leveller - 20kg Bag & 4 Litre Bottle
Ultra Tile Pro Level Two - High Flow Floor Leveller - 20kg Bag & 4 Litre Bottle
Ultra Tile Pro Level Two is a general purpose mid strength two-part smoothing underlayment. Its exceptional flow characteristics make it a very easy material to apply.
Don't know how much levelling compound you need? Click here for our handy levelling compound calculator.
Ultra Tile Fix Pro Level Two is a mid-strength smoothing underlayment. A two-component system consisting of a powdered blend of cements, graded fillers and additives, and a pre-gauged polymer liquid. Tiles can be applied to the internal subfloors in as little as 24 hours. Its fast set time (in good ambient conditions) enables light foot traffic in 2.5 hours.
SUITABLE SURFACES & SUBSTRATES
- Concrete subfloors
- Tamped or pan floated concrete
- Sand / cement screeds
- Existing smoothing underlayments
- Terrazzo / granolithic ceramic tiles
- Anhydrite / calcium sulphate / gypsum based screeds
- Plywood / tile backer board
- Warm water underfloor heating
- Radiant electrical underfloor heating system
- Vinyl tiles
- UltraFloor DPM IT
- Presmoothing prior to DPM or MVS
COVERAGE
Applied Thickness | Coverage Per Unit (approx.) | Consumption Per 10m² Area |
2mm | 6.0m² | 1.7 bags |
5mm | 2.4m² | 4.2 bags |
10mm | 1.2m² | 8.4 bags |
30mm | 0.52m² | 19.2 bags + 8.1 x 10kg units aggregate |
TECHNICAL DATA
- Unit Size: 20kg Bags & 4 Litre Bottle
- Depth: 2 - 15mm
- Working Time at 20 degree celsius: *20 - 30 Minutes
- Walk on hardness time at 20 degree celsius: *2.5 Hours (3mm Application)
- Commence the tiling process: 24 Hours (2-15mm Application (* Depending on substrate porosity, nature of flooring and note in Curing & Drying above)
- Compressive Strength (N/mm): 28 Days: 25.0 (to BS EN 13892-2)
- Flexural Strength (N/mm): 28 Days: 5 (to BS EN 13892-2)
SURFACE PREPARATION
Assessment: All subfloors should be protected from moisture from the subground by use of a base damp proof membrane (DPM) (please check older properties, which may not have a base DPM and consult Ultra Tile Fix for advice). Assess moisture levels in accordance with BS 8203, to achieve a hygrometer reading of 75 % RH or less. Where this is not attained a surface DPM should be used – the selection of which will be subject to the subfloor (please seek advice from Ultra Tile Fix). Any surface laitance, adhesive residue, paints, weak smoothing underlayments and any other materials which will hinder Ultra Tile Fix Pro Level Two bonds with the subfloor should be mechanically removed. The subfloor should be clean, dry and sound. The area should also be dust free prior to any primer application.
PRIMING
All ratios are water to primer. Subfloors should always be primed. Primer should be allowed to dry prior to the application of Ultra Tile Fix ProLevel Two. Drying times will be based on ambient conditions - bear in mind that cold or damp / humid conditions, or poor airflow, can extend drying time (please see Ultra Tile Fix Pro Primer datasheet for further information).
Porous Substrates:
The absorbency of floors / screeds can vary significantly, this is to be assessed by personnel on site. Apply a coat of primer diluted 3 parts water to 1 part primer. Allow to completely dry (usually 1 - 2 hours). Apply a second coat diluted 1 part water to 1 part primer and allow to completely dry before applying further materials. Note: on very absorbent substrates a third coat may be required diluted 1 part water to 1 part primer.
Non-porous Substrates:
Including very dense substrates/subfloors. Ultra Tile Fix Pro Primer should be applied neat, in a thin uniform coating and allowed to dry fully.
SUBFLOOR PREPARATION: WHICH SUBSTRATE?
Concrete Subfloors:
Power floated concrete should be treated as nonporous. Mechanically abrade (shotblast or scarify) to remove surface hardeners and expose the cement / aggregate. Apply Ultra Tile Fix Pro Primer neat in a thin uniform coating, allowing it to dry fully (usually 1 - 2 hours).
Tamped or Pan Floated Concrete:
Should be treated as porous, and any laitance or weak material should be mechanically removed to ensure a sound, dry and dust-free surface. Apply Ultra Tile Fix Pro Primer diluted 3 to 1 with clean water and allow to dry fully (usually 1-2 hours).
Sand/Cement Screeds:
These should be strong enough for an application of Ultra Tile Fix Pro Level Two. Weak, friable or damaged screed should be uplifted and repaired. Apply Ultra Tile Fix Pro Primer diluted 3 to 1 with clean water and allow to dry fully (usually 1-2 hours). Two-coat application may be required for very absorbent screeds.
Existing Smoothing Underlayments:
Ultra Tile Fix ProLevel Two can be used over most intact cementitious cement underlayments. Remove adhesive residues and treat as an absorbent floor. Apply Ultra Tile Fix ProPrimer diluted 3 to 1 with clean water and allow to dry fully (1 - 2 hours). Apply a second coat diluted 1 to 1 with clean water allowing it to dry to a clear film (1 - 2 hours). Note: application is only suitable on subfloors that are in equivalent strength to Ultra Tile Fix Pro Level Two.
Terrazzo/Granolithic Ceramic Tiles:
These must be securely bonded, and any surface treatment should be mechanically removed. A good mechanical key should be ensured by abrading the surface using a Surface Texturing & Grinding (STG) machine (a diamond disc is recommended). These subfloors can be treated as low porosity and primed using Ultra Tile Fix ProPrimer neat.
Calcium Sulphate/Anhydrite/Hemihydrate Screeds:
See relevant manufacturer’s technical datasheet. A barrier primer application is required. If moisture is above 75 % RH we do not recommend using a surface DPM. These screeds often incorporate warm water underfloor heating systems which can be used, along with dehumidifiers, to speed up the drying process. Screed manufacturers normally suggest this can be conducted after 7 days minimum curing. Mechanically remove any laitance or weak material to leave a clean, dry and dust-free surface. We recommend an STG machine with suitable mesh grinding disc of 60 - 100 grade grit. Apply Ultra Tile Fix Pro Primer diluted 3 to 1 with clean water and allow to fully dry overnight. Apply a second coat diluted 1 to 1 with clean water allowing it to dry to a clear film usually 1 - 2 hours.
Plywood/Tile Backer Board:
Plywood must be of flooring grade and mechanically fixed to a sound strong base. Ultra Tile Fix Pro Level Two is only recommended for use with plywood of 15mm thickness and greater. Tile backer boards of 6mm thickness. Plywood must be sealed on the underside and along all edges to ensure moisture absorption from beneath is kept minimal. For thinner flooring grade plywood subfloors contact Ultra Tile Fix technical department. Plywood and tile backer board absorbency differs depending on the nature of the surface. Normally a diluted coat of Ultra Tile Fix ProPrimer (3 to 1 with clean water) is recommended. For dense surfaces of very low absorbency apply Ultra Tile Fix ProPrimer neat in a thin uniform coating. Allow primer coats to fully dry.
Warm Water Underfloor Heating (UFH):
Systems must have been fully commissioned and brought up to their maximum temperature, and ideally switched off 48 hours before application. In the absence of other heat sources, the UFH may be set to cutback position to achieve an air temperature of 15 degree celsius. Any expansion or movement joints must be carried through to the floor covering surface.
Radiant Electrical Underfloor Heating System:
Ultra Tile Fix ProLevel Two can also be used over electrical UFH systems where the cables are fixed to a sound strong mechanical fixed cement faced backer board. Apply Ultra Tile Fix ProPrimer diluted 3 to 1 with clean water and allow to dry fully (usually 1-2 hours). It may also be used where electrical UFH is used over cementitious or calcium sulphate subfloors. Priming should be as per the substrate. In all cases Ultra Tile Fix Pro Level Two must be applied at a thickness of 5mm above the cables for resilient, textile and timber applications and a minimum of 3mm for application of stone, ceramic or porcelain products.
Vinyl Tiles:
Not all vinyl tile flooring is suitable to be levelled/tiled over. Cushioned or flexible vinyl tiles should not be overlaid and must be removed along with the adhesive residue. Hard vinyl tiles should be lightly abraded and then primed with Ultra Tile Fix Pro Primer neat.
UltraFloor DPM IT:
Applications should be carried out within 36 hours of DPM application (see DPM IT datasheet). The DPM must then be primed with Ultra Tile Fix Pro Primer neat in a thin uniform coating, allowing it to dry fully (usually 1 - 2 hours).
Pre-smoothing prior to DPM or MVS:
Ultra Tile Fix Pro Level Two can be used to on cementitious subfloors with residual moisture > 75 % RH to pre-smooth prior to applying an Ultra Floor epoxy DPM. Prepare the subfloor to leave a lightly textured dust free surface. Either prime with Ultra Tile Fix Pro Primer diluted 3 to 1 with clean water and allow to fully dry or lightly dampen with clean water, allowing the surface to matt off. This will reduce pinholing. Note: presmoothing of subfloors where there is an absence of a base DPM can be carried out provided there is no risk of hydrostatic pressure, and all previous materials have been removed to leave the cementitious base. If in any doubt always apply the DPM directly to the original subfloor.
For any other scenarios please call Ultra Tile Fix Technical Services for advice.
MIXING & APPLICATION
Shake the pre-gauged bottle of liquid prior to opening. Pour the entire contents of the liquid into an oversized bucket (20 litres or more capacity). Gradually add the powder whilst continually mixing using an electric drill fitted with a power whisk, suitable for use with cement materials. After completely adding the powder, continue mixing for a further 2 minutes, keeping the whisk below the surface of the product to minimise air entrainment, until a lump free creamy material is attained. Ultra Tile Fix Pro Level Two should only be mixed as single units. Do not add further liquid or water. Pour onto the floor and spread with a smooth edge steel trowel. Ultra Tile Fix Pro Level Two has exceptional flow characteristics, a spiked roller may be used to further improve the finish particularly between adjacent units of product. Only spike roll whilst the product is still in its fluid state (immediately due to the limited workability and rapid setting nature).
CURING & DRYING
All curing and drying times are based on good site conditions, air temperature of 20 degree celsius, air humidity of maximum 75 % and good ventilation. Cold, humid or damp sites, or those with poor airflow, will prolong curing and drying times, so make adequate allowances for such. Avoid strong drafts and direct sunlight during curing which can force dry the product and result in excess tension and cracking. Ultra Tile Fix Pro Level Two is ready to receive light foot traffic after 2.5 hours. Once this leveller has been installed it must be ensured that it is fully dry before continuing the tiling process, to include priming and adhesive applications.
CLEANING
Tools should be thoroughly cleaned with water to remove excess material immediately after use and before adhesive sets.
POINTS OF NOTE
All Ultra Tile Fix levellers are manufactured to meet the performance requirements of BS EN 13813 and the relevant classifications.
STORAGE
This product must be stored in unopened bags, clear of the ground in dry conditions. Avoid frost. Ideal storage temperatures are between 5 degree celsius and 25 degree celsius
SHELF LIFE
Under the above storage conditions this product has a shelf life of 8 months. High temperatures and high humidity will lead to a reduced shelf life.
HEALTH & SAFETY
Please ensure that appropriate PPE is used when preparing, mixing and applying products. Always wash hands before consuming food and make sure that materials are kept safely out of reach of children and animals. Please dispose of packaging and waste appropriately. A full Material Safety Data Sheet relating to this product is available from ultratilefix.co.uk.
QUALITY ASSURANCE
All products are manufactured in a plant whose quality management system is certified as being in conformity with BE EN ISO 9001. Ultra Tile Fix products are guaranteed against defective materials and manufacture and will be replaced or money refunded if the goods do not comply with our promotional literature. We cannot however accept responsibility arising from the application or use of our products because we have no direct or continuous control over where and how our products are used. All Ultra Tile Fix products are sold subject to our terms and conditions of sales, copies of which may be obtained upon request.